ChirpyToday at 6:13 PM
@,,robbs a piece of bed frame or angle iron works really well for a dross scoop if nothing else, lol
[6:14 PM]
I have three dross scoops, but technically the one is a slag scoop instead
[6:16 PM]
the one is just some 1/2" OD rebar that has a slit cut in the end and a piece of flat bar welded in it, I use that for aluminum, the second is some angle iron that's been welded to a piece of 3/8" bar and the side away from the bar is shaped round so it matches the side of the crucible, then a bunch of 1/8" holes drilled in it for the metal to flow through it, which I use for brass/bronze, and the last is just a piece of bed frame to scoop the slag off the iron because the iron will physically eat any steel you put into it, so it was quick, easy, and disposable, lol
[6:18 PM]
and @Tek, I wasnt laughing at you, I was just saying that until you have alot more experience with molten metal, iron shouldnt even be on the playing field
[6:19 PM]
aluminum, something happens, you can get hurt pretty badly, brass, bronze or copper, something happens, and you end up perminantly disfigured, iron on the other hand will just plain kill you
[6:20 PM]
something that high of temp, and that extreme isnt something someone just doing aluminum castings, it isnt something I would recommend at all
[6:20 PM]
the temps, the materials, the safety equipment, furnace build, etc is all completely for iron
[6:21 PM]
it's like comparing melting lead to melting bronze, and actually that much of a temperature jump
[6:22 PM]
I have a heavy shirt on, a jacket on, and a thick leather apron on, and it will burn the hairs off of your chest through all of that
[6:23 PM]
pouring shank and crucible tongs have to have heat shields on them, you have your hand near the crucible for more than 20-30 seconds while trying to pour, you will end up with between first and second degree burns to your hands, just off of the radiant heat off of the crucible
[6:24 PM]
Ive burnt my face a few times, you have to have a beard on or some face covering, or it will burn your face from the heat radiating from the furnace
[6:24 PM]
if you can get past all of the heat and get everything done up right, then there's still all the metalurgy
[6:25 PM]
there's around a dozen grades of cast iron, all have different melting points, different flow properties, different shrinkage, etc, and just melting iron is completely different than pouring it
[6:26 PM]
the melting point of really good quality cast iron is around 2400F, pouring temp is around 2600-2800F depending on the thickness and the alloy your using, so your furnace has to be pumping out at least 3000F consistantly and be tuned absolutely perfect
[6:28 PM]
the slag that forms on the top of the melt, if you have the atmosphere just right, it wont build up much, but it'll actually form a shell on top of the iron that looks like the metal is chilling, but the slag just hardens, you have to break through that from time to time to keep it from building up too thick, or you have to hammer through it with a poker rod, and that's just asking to break the crucible with a molten crucible full of iron, or at least knocking it over in the furnace, destroying your furnace
[6:29 PM]
a friend of mine had that happen to him and he ended up with molten iron hitting his leg, even with the chaps and everything on, just the tiny bit that hit him, he had to go for skin graphs a few times to deal with the amount of damage to his leg
[6:30 PM]
he has a business and pours iron castings, so he's around it all the time and knows what he's doing
[6:32 PM]
on top of that, you need to have the right type of cast iron, just any type of iron wont work because some is designed to chill like crazy and turn to white iron, some are designed for ductile stuff, some is for art stuff which has a lower melting point and is alot more fluid, and other is more for making parts out of that are strong, like what you would make a lathe out of
[6:33 PM]
mixing them up will end up with an alloy that would have hard spots all throughout it and be pretty much impossible to machine up
[6:35 PM]
now you have to keep an eye on the metalurgy of the iron also because if it has phosphor in it, it'll flow really nicely and melt at a lower temp, but you'll end up with hard spots in it and it will be kinda weak, if it has sulfur in it, it'll be so thick to pour that it'll be like trying to pour honey and wont flow, if it has other alloying elements in it, it can form carbides with those alloys, which then you cant cut through it to machine it or drill it
[6:36 PM]
you need just the right amount of ferrosilicon for the amount of iron, too much and you'll have insane amount of shrinkage to the metal and the parts will be extremely weak, too little and you'll end up with hard spots and chilling of the parts
[6:38 PM]
the iron also needs to be treated differently than aluminum, brass, bronze, etc castings, it cant be broken out of the molds until it is completely cool, and even smaller castings can take a day or so to completely cool in the mold, otherwise it'll have so many stresses in it that you go to cut it and it'll bind up saw blades, destroy drill bits, taps, etc from it moving as your trying to work with it, and opening the mold too soon, you'll end up with a part that will chill or break just from the part cooling too fast
[6:39 PM]
Ive seen a few that actually will crack and break into pieces from being opened from the mold right away
[6:40 PM]
the furnace, burner, and everything has to be just perfect, otherwise you wont be able to reach the pouring temps
[6:41 PM]
and the sand has to be specially made for iron, which will have a low sulfur based coal dust in it commonly called sea coal in it, which lifts the iron up off of the surface of the sand till it can form a skin, which keeps the iron from burning into the sand and keeps the sand from physically melting to the iron castings
[6:43 PM]
if you can get through all of that, you can try iron, but just be aware that a percentage of the iron actually gets lost to slag, much more than you have for any other metal, and you also have to be careful trying to scoop the slag and everything because the iron as it's close to pouring temps, will actually spit, which will throw slag at you and all over the inside of the furnace, so you have to have some seriously good safety gear to deal with that
[6:44 PM]
that's iron in a nutshell, lol
[6:44 PM]
so unless your absolutely sure you know what your doing with the casting stuff, dont mess with iron, lol
[6:47 PM]
and @,,robbs, there really is no good diy mix for investment casting for dipping, I know there's a commercial stuff called suspend a slurry I think, or something like that, and if your really getting into it to do statues and larger art stuff, it would be better to just get some of it since it goes a very long way, but if your just doing smaller stuff, I would look into a block type investment tbh
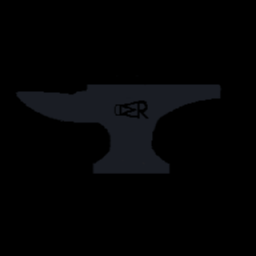
Lord of Lava Island 🌋🤷🌋Today at 6:51 PM
Information overload!
ChirpyToday at 12:50 PM
@Dusty Dan I use some bitiuminous coal that I had here, it was full of of iron pyrite and sulfur, but I crushed it up to a really small size, then put it in a bottle and filled it up with water
[12:51 PM]
if you shake it really well, the pyrite and less pure coal will sink to the bottom since it's heavier and the cleaner coal will be last to fall
[12:51 PM]
I only added around 1/4 of the bottle of coal to water
[12:52 PM]
with it being that small of a size, it takes a very long time for it to all settle out
[12:54 PM]
you can also buy the sea coal dust from lancaster foundry supplies
[12:55 PM]
Ive also seen people adding in wood flour instead, but I expect that it would choke everything up pretty badly over time
No comments:
Post a Comment