Keep forgetting this so I am posting it for myself
70% baby oil, 30% tiki torch fuel
smokes like crazy but reduced tool pressure
Tuesday, November 24, 2020
Tiki Torch Oil for cutting
Sunday, November 15, 2020
Monday, November 9, 2020
Determine aluminum pouring temperature with a steel rod
Have always heard about using a steel rod for checking aluminum temperature but never to this level of detail.
ChirpyYesterday at 7:05 PM
yea, those things are useless tbh
[7:05 PM]
next time, take a steel rod and stick it in the exhaust to heat it up for 10 seconds, then stick it into the metal to the bottom
[7:06 PM]
if it balls up on it, then it's too cold, if it sticks to it but easily fall off as a thin shell of aluminum, then that's perfect pouring temp for most castings, if it repels it like a magnet, then it's way too hot
And on Dec 7th
ChirpyToday at 3:33 PM
for thin castings in aluminum, you want it to be silver in daylight, but might have a little color to it in the furnace
[3:33 PM]
it shouldn't stick to a preheated steel rod, but shouldn't repel it like a magnet either
[3:34 PM]
I mean it shouldn't ball up on the steel rod, if it forms a super thin skin on it that easily falls off, then your good to go usually, or that gives you a good place to start from
Dusty DanToday at 3:58 PM
@Chirpy are we talking about a 1/2" or so rod ?
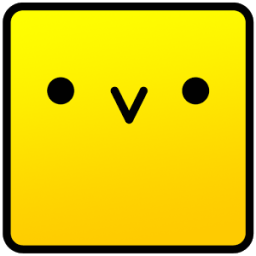
ChirpyToday at 3:59 PM
for what?
[3:59 PM]
oh, I usually just have a 3/8" rod or whatever, the bigger it is, the longer you have to preheat it
[3:59 PM]
other than that, i dont think it really matters tbh, lol
[4:00 PM]
I have some 3/8" rod and thats what I use just to poke the melt
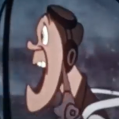
Dusty DanToday at 4:00 PM
OK thats what I wanted to know
Saturday, November 7, 2020
Weld Positioner
Made the plate on the sidney. Cut the center with a 1 1/2" hole saw mounted in the tail stock. The bored it out to 2". Cut the grooves with a carbide V bit. Could not tripan the outer edge so I cut it with an angle grinder. The plate is a bit warped anyway. Plant to cast and machine an aluminum one.
About to cut the bolt circle on the hub. Found out I can't use the 6 jaw chuck on the dividing head. Too much unthreaded area. Lost the light. Start here tomorrow.
Used the special nuts I made to bolt the Master Mill to the Sidney compound circle to hold the dividing head to the drill press table.
Still need to set the drill position. I think I can do that by manipulating the table. Rotation and left/right.
Sunday
Working on the order of operations for drilling the bolt circle in the hub and plate. The hole circle and dividing head are new to me so I need to think it out. Going to need to switch between center drill, drill, tap, and in case of the alignment pin a reamer. Given that this is a round column drill press that is a problem. Thinking the alignment hole can be hand reamed without the dividing head after the other holes are drilled and tapped.
There will be 4 or 5 1/4" 20TPI bugle head screws and one 3/8" hole for an alignment pin used to reposition the hub for drilling additional plates.
- Position plate on hub
- Center drill alignment hole
- Drill the 3/8" - 1/64", 23/64" alignment hole through plate and hub
- Insert drill to lock plate to hub.
- Center drill screw positions in plate
- Drill 1/4" clearance sized holes in but not through plate screw positions.
- Remove plate
- Finish drilling screw holes on 2nd drill press
- Center drill hub for screw holes
- Drill the #7 machine screw holes, tap size for 1/4" 20TPI
- Tap the screw holes
- Place plate on the hub using drill bit for alignment
- Counter sink screw holes in plate using depth stop
- Remove hub from dividing head.
- Ream the alignment hole in the plate and hub in one operation: why not stay with drill bit?
- Replace the hub on the dividing head using the alignment pin.
- Position the plate on the hub again using the pin.
- Center drill the machine screw positions.
- Remove the dividing hub from the drill and clearance drill the 1/4" screw holes.
- Counter sink the screw holes.
Monday
Tapped the holes with a tap from a set from TSC's tool assortment table. Not a good move. Ended up snapping off a thread chaser in one of the 4 holes. Went over the remaining 3 holes with the tap from my old set and ended up with an inch of useable thread. Works with 3. Good enough.
Cut off the machine screws and counter sunk the plate for the heads. Table has about 50 thou of unevenness near the edge. That is noise level in terms of an arc distance so I am not going to worry about it.
Using the large drill, aka mud mixer, I can run the table at about .5 RPM. This maybe to fast for a 4 inch pipe and is for larger diameters. Net says 3-6 inches per minute. .5 is right at 6. I have a 2:1 box I could add between the drill and the gearbox but will try it without first. Would need to make an adapter. Maybe best cast one that mimics what is used between the first 2 boxes.
I may have the ground figured. According to someone on the net dragging a mig tip instead of a copper brush works. Going to try that first. In it fails most of it can be used with a brush setup.
![]() | ![]() |
Extension and spring. | Shoe |
Added a bit of flat stock at a right angle to the aluminum angle to gain clearance and position it closer to parallel to the table.