ChirpyToday at 6:11 PM
hi
[6:13 PM]
the salt works because the salt is really agressive to oxides when molten, thats why if you use a salt flux in pottery and try firing it, it'll just tear the lining apart and eat it to no end, which alot of those bricks are made of aluminum oxide
[6:14 PM]
the 50/50 mix works because sodium chloride melts at 1450F, potassium chloride melts at 1500F, but when they melt together, they form an eutectic which melts at around 1000F
[6:15 PM]
there are different salts that you can add to that mix to drop it even lower, which is handy for dropping it down to the temp that zinc alloys can use
[6:15 PM]
@Dusty Dan @Helpful Hardware Professor
[6:15 PM]
and no need to add anything else to the flux tbh for aluminum, those two work perfectly fine
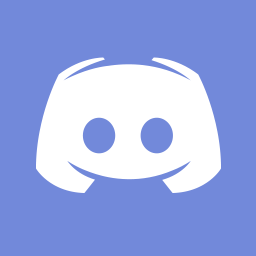
Paul JoatToday at 6:16 PM
So do you melt the salt together before using it as flux then?
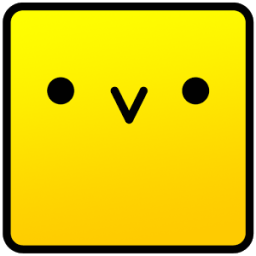
ChirpyToday at 6:16 PM
when they're really fine like you find in the containers of morton's lite salt, the grains are close enough together and well mixed enough that it can react with each other when it's in contact with the metal